Browse
Dealer
Electric Car Conversion Motors
D&D Motor Systems is the premier manufacturer of electric DC
motors in the U.S., specializing in gas to electric car conversions. Our high-performance electric car motors offer
superior torque, enhanced thermal capabilities, and a competitive price, all while being proudly made in the USA.
Whether you're looking for an electric car motor for sale, a best-in-class EV motor, or a reliable motor for an
electric car conversion, we have you covered.
Additionally, we offer a complete line of U.S. made 72V electric DC controllers designed specifically for use with
our DC electric vehicle motors. Explore our products for your DIY electric car conversion kit, gas to electric car
conversion, or even a VW Bug EV conversion project.
Lower Performance
Part Number: 170-004-0003 (Series)
Description: This EV Motor is good for small cars weighing between 800 - 1500 lbs and looking for low performance. Good for someone looking for a low cost option to commute a short distance to and from work or to just run short errands around town. Vehicle designs usually are between 48 and 96 Volts.
|
EV Car Motors Specifications
Design Parameters | |||||||
---|---|---|---|---|---|---|---|
Full Load Weight (lbs) | Voltage | Gear Ratio | Batteries/ Usable energy | Tire Size (Inches) | |||
800 | 72 | 3 | 5.4 KWh | 19 | |||
1100 | 72 | 3 | 5.4 KWh | 19 |
Motor Performance and Characteristics | ||||||
---|---|---|---|---|---|---|
PS | HP (Peak | Continuous) | Max Efficiency | Enclosure | |||
6 | 18.5 | 8.5 | 83 | Vented | |||
6 | 18.5 | 8.5 | 83 | Vented |
Vehicle Performance | |||
---|---|---|---|
Top Speed (mph) | Contoller Amperage (Amps) | Acceleration | Range (Miles) |
60 | 600 | Moderate | 20-50 |
60 | 600 | Low to Moderate | 15-40 |
Other Available Motor Options: Low/Medium Performance Motor Options
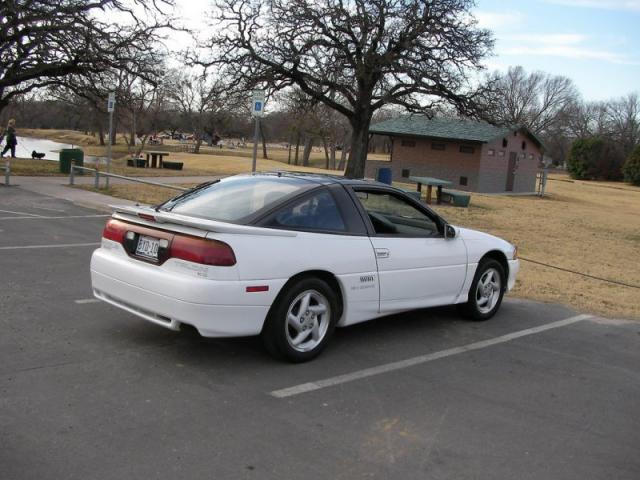
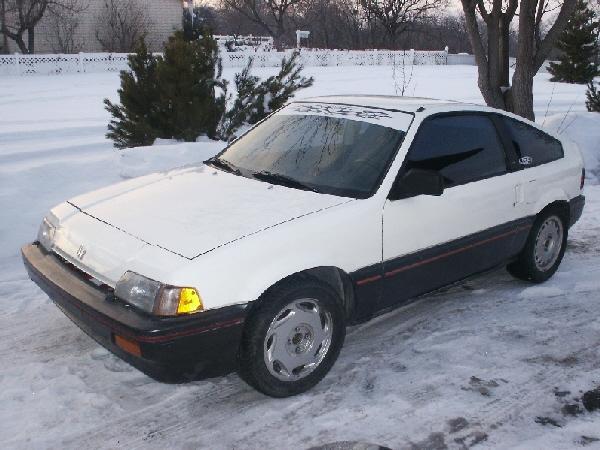
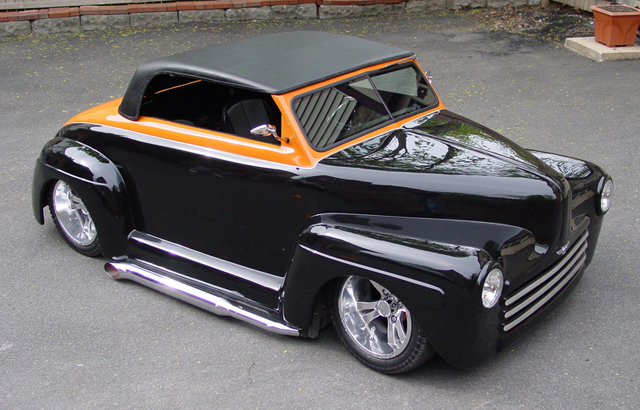
High Performance
Part Number: 170-015-0004 (Series)
Description: This EV Motor is good for small cars weighing between 1000 - 1800 lbs and looking for medium performance. Good for someone looking for a mid range cost option to commute a short distance to and from work or to just run short errands around town while getter better performance than our 170-015-0004 option. Vehicle designs usually are between 72 and 144 Volts.
|
EV Car Motors Specifications
Design Parameters | |||||||
---|---|---|---|---|---|---|---|
Full Load Weight (lbs) | Voltage | Gear Ratio | Batteries/ Usable energy | Tire Size (Inches) | |||
2000 | 72 | 3 | 5.4 KWh | 19 | |||
2000 | 96 | 3 | 7.2 KWh | 19 | |||
2000 | 120 | 3 | 9.0 KWh | 19 | |||
2000 | 144 | 3 | 10.8 KWh | 19 |
Motor Performance and Characteristics | ||||||
---|---|---|---|---|---|---|
PS | HP (Peak | Continuous) | Max Efficiency | Enclosure | |||
16 | 19 | 8.4 | 86.5 | Vented | |||
16 | 30.4 | 10.2 | 85 | Vented | |||
16 | 37.3 | 12.4 | 84 | Vented | |||
16 | 43.8 | 14.6 | 82.4 | Vented |
Vehicle Performance | |||
---|---|---|---|
Top Speed (mph) | Contoller Amperage (Amps) | Acceleration | Range (Miles) |
70 | 600 | Low | 10-20 |
70 | 600 | Moderate | 14-25 |
70 | 600 | High | 17-35 |
70 | 600 | High | 20-45 |
Other Available Motor Options: High Performance Motor Options
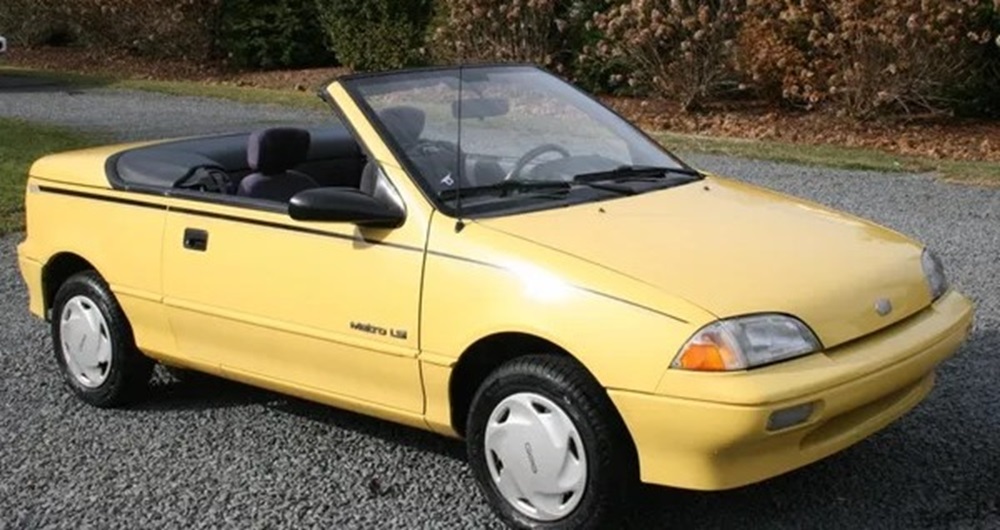
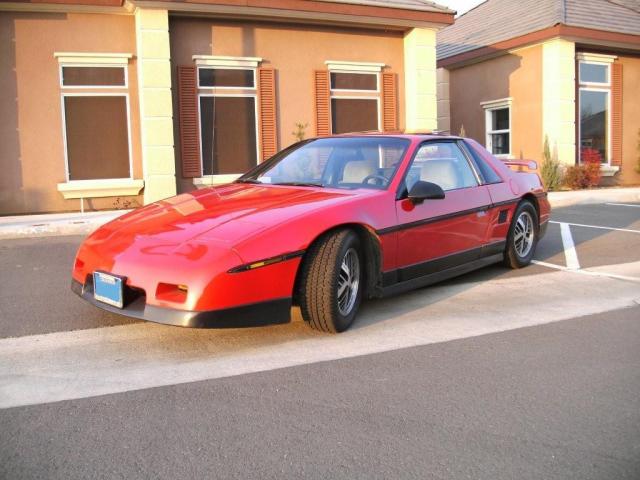

Need a Custom Car Motor?
1. Why build an EV?
Today there are limited production electric vehicles (EVs) available, so
converting an existing internal combustion engine (ICE) vehicle to an electric vehicle (EV)
might be the best choice available to obtain an EV. Building your own electric vehicle
(EV) can be a rewarding and challenging experience. Not only will you be a pioneer in the
EV movement, but you will also be recycling a car that may be headed for the junk yard. Don’t
wait for Detroit. Custom build an EV yourself. A typical EV conversion will
achieve a range of 30-60 miles per charge. Studies show 80% of commuters travel less than 40 miles per day,
making a gas to electric car conversion a practical solution for daily use.
EVs are a clean, efficient alternative to conventional vehicles – using readily available
electric car motors, often included in a diy electric car conversion kit.
EV motors produce zero emissions and, over the full fuel cycle, are up to 99% cleaner than
gasoline and diesel vehicles. Electric car engine owners enjoy significantly lower fuel and
maintenance expenses. Finally, EVs help reduce our dependence on oil.
D&D Motor Systems does not provide
complete electric vehicle (EV) conversion kits. We only provide the motor
and controller—ideal for those looking for the best electric motor for car
conversion or standalone electric car motors for sale. To obtain complete kits
or other components go to our
Links
section and look under EV
Conversions for potential suppliers.
2. What basic steps are involved
- Define the purpose of the vehicle:
- Why do you want an EV?
- Where will you drive it?
- Who else will drive it?
- How many miles do you require on a daily basis?
- How often will you drive the vehicle?
- With or Without passangers?
- Will your employer allow you to charge at work?
- How much do you want to spend?
- How much time do you have for the conversions?
- Evaluate the vehicles manufactured.
- Sports cars, such as the Honda CRX, Pontiac Fiero, Toyota MR2, Porsche 914, Fiat X-19, Nissan Pulsar, MGB or MG Midget. Sports cars have limited space and minimal payload capacity.
- Passenger cars and vans, such as the Ford Escort, VW Rabbit, VW Beetle, Saturn, Honda Civic and Geo Metro. The payload capacity for a Geo Metro is about 600 lbs.
- Select a Vehicle to Convert
- Look for an EV kit for the vehicle you choose
- Familiarize yourself with the EV parts
- Safety Testing
Ask yourself the following questions:
When you start to evaluate the different vehicles, you will find there are mainly 2 classes out there:
Each of these classes have their own characteristics with respect to aerodynamic drag, curb weight, Gross Vehicle Weight Rating (GVWR), passenger compartment, and available space for batteries. Table 1 lists typical vehicles under each of these classes and their range using various lead acid battery packs (6V and 12V). Range is a function of battery weight because the battery represents the fuel. Typically it takes 15-20 lbs of lead to achieve 1 mile in range. A Rule of Thumb is that 1/3 of the EVs weight should be batteries; the other 2/3 represents dead weight (i.e. frame, suspension, body, motor, etc). If you could decrease this dead weight to 1/2 leaving 1/2 for fuel, you would have superior performance.
|
Other Considerations:
Front Wheel Drive(FWD) vs Rear Wheel Drive (RWD)
A FWD vehicle has the advantage of being more efficient, improving range in most electric car motor setups. However, front-wheel-drive vehicles often have smaller engine compartments, limiting battery placement. Also, FWD vehicles require more weight on the front axle. Rear-weighted EV motor systems in RWD cars may offer better handling in snow or rain, as seen in classic VW Bug EV conversions.
High-voltage, high-amperage EV motors can produce more torque than the original ICE engine. For smaller FWD cars, this can lead to traction issues. That’s why diy electric car conversion kit users often prefer RWD platforms for better weight distribution and handling.
Manual Vs. Automatic Transmission
Most EV conversion vehicles use manual transmissions, which are more efficient than
automatics. Manual transmissions require less torque from the electric car motor, extend
driving range, and eliminate the need for a cooler. Because most electric car motors operate
efficiently at 4000–5000 rpm, automatics—which shift around 2000 rpm—aren’t ideal. If you're working on a
diy EV motor project, we recommend switching to manual.
Power Brakes
As your vehicle gains 800–1200 lbs from the EV conversion parts (e.g., dc motors for
cars and batteries), power brakes are recommended for safety. Curb weight and GVWR
become key when selecting a donor vehicle for your gas to electric car conversion.
For example, a Geo Metro is light but has a low payload capacity. While it’s a popular platform for hobbyists, heavier systems like those using NetGain Motors or high-performance EV motors may strain the vehicle's frame. Always check weight distribution, especially with onboard chargers and battery box placement. Rear-heavy layouts, such as in a VW Bug EV conversion, can improve snow handling.
These kits make the process easier and include all components except batteries. A typical diy electric car conversion kit costs between $3,000 – $6,000. Battery costs vary from $700 – $4,000 based on size and chemistry.
From electric car motors for sale to chargers and wiring, knowing your system is essential. Many users prefer kits with dc motors for cars for simplicity and affordability.
Test the EV motor setup, charger, and connections. Once complete, enjoy the quiet ride and performance. Whether you’re using parts from NetGain Motors or your own custom design, your diy EV motor setup will deliver a cleaner, more efficient drive.
3. How much does it cost to complete a typical conversion
Obviously this firstly depends greatly on the vehicle you looking to convert and what you pay for that vehicle. Secondly, the overall performance and range you require in your application are major price effectors. With that said, the range could be anywhere from $4,500 to $11,500 typically.
4. How much will I save on gas?
Vehicle Type | Description | Details |
---|---|---|
Gas Guzzler | Mileage | 20 miles/gallon |
Cost Per Gallon | $4.00 (US Average) | |
Cost Per Mile | $0.20 / mile | |
Clean Electric | Electricity Cost | $0.07 / kWh |
Recharge Cost | Approx. $0.84 / charge (12 kWh) | |
Vehicle Range | Approx. 50 miles / charge | |
Cost Per Mile | 1.68 cents / mile | |
Savings | Savings Per Mile | $0.1832 / mile |
Annual Miles Driven | 12,000 miles / year | |
Annual Savings | $2,198.40 / year | |
Note: Annual savings do not include reduced maintenance costs. You could save even more! |
5. What are the most popular EV conversion vehicles
![]() |
![]() |
![]() |
![]() |
![]() |
![]() |
6. What driving range can I expect per charge
Of course it all depends on the conversion – vehicle type along with the number and type of batteries. However, most people who drive electric street vehicles say they get between 30 and 60 miles per charge, without saying what they mean by charge. I believe it is only reasonable to state the range based on a 50% drop in charge capacity. You can go lower, but repeatedly going down to 40% and less capacity (remaining capacity) point will shorten the life of the batteries. Keep in mind that driving habits impact distance. For more detailed information regarding vehicle range, go to FAQ #2 - Section B, above.
7. How fast will my converted EV go
Depending upon your vehicle type, set-up and application the average top speed is anywhere between 30 - 70 MPH (miles per hour)
8. How do electric cars work
Electric cars are something that show up in the news all the time. There are several reasons for the continuing interest in these vehicles:
- Electric cars create less pollution than gasoline-powered cars, so they are an environmentally friendly alternative to gasoline-powered vehicles (especially in cities).
- Any news story about hybrid cars usually talks about electric cars as well.
- Vehicles powered by fuel cells are electric cars, and fuel cells are getting a lot of attention right now in the news.
An electric car is a car powered by an electric car motor rather than a gasoline engine.
From the outside, you would probably have no idea that a car is electric. In most cases, electric cars are
created
by converting a gasoline-powered car, and in that case it is impossible to tell. When you drive an electric car,
often the only thing that clues you in to its true nature is the fact that it is nearly silent.
Under the hood, there are a lot of differences between gasoline and electric cars:
- The gasoline engine is replaced by an electric motor .
- The electric motor gets its power from a controller .
- The controller gets its power from an array of rechargeable batteries .
Inside an Electric Car
The heart of an electric car is the combination of:
- The electric motor
- The motor controller
- The Batteries
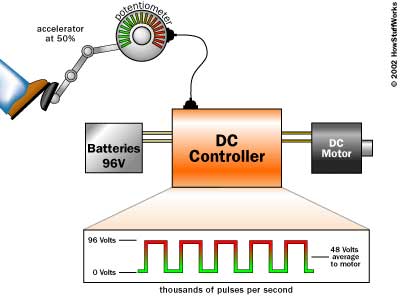
A simple DC controller connected to the batteries and the DC motor. If the driver floors the accelerator pedal, the controller delivers the full battery voltage to the motor. If the driver takes his/her foot off the accelerator, the controller delivers zero volts to the motor. For any setting in between, the controller chops the battery voltage, thousands of times per second to create an average voltage somewhere between 0 and Full Battery pack voltage.
The controller takes power from the batteries and delivers it to the motor. The accelerator pedal hooks to a
potentiometer (variable resistor), and this potentiometer provides the signal that tells the controller how much
power it is supposed to deliver. The controller can deliver zero power (when the car is stopped), full power
(when
the driver floors the accelerator pedal), or any power level in between.
The controllers job in a DC electric car is easy to understand. Let us assume that the battery pack contains 12
12-volt batteries, wired in series to create 144 volts. The controller takes in 144 volts DC, and delivers it to
the motor in a controlled way.
The very simplest DC controller would be a big on/off switch wired to the accelerator pedal. When you push the
pedal, it would turn the switch on, and when you take your foot off the pedal, it would turn it off. As the
driver, you would have to push and release the accelerator to pulse the motor on and off to maintain a given
speed.
Obviously, that sort of on/off approach would work but it would be a pain to drive, so the controller does the
pulsing for you. The controller reads the setting of the accelerator pedal from the potentiometers and regulates
the power accordingly. Say that you have the accelerator pushed halfway down. The controller reads that setting
from the potentiometer and rapidly switches the power to the motor on and off so that it is on half the time and
off half the time. If you have the accelerator pedal 25 percent of the way down, the controller pulses the power
so it is on 25 percent of the time and off 75 percent of the time.
Most controllers pulse the power more than 15,000 times per second, in order to keep the pulsation outside the
range of human hearing. The pulsed current causes the motor housing to vibrate at that frequency, so by pulsing
at
more than 15,000 cycles per second, the controller and motor are silent to human ears.
Most DC controllers used in electric cars come from the electric forklift industry.
Electric Car Motors & Batteries
If the motor is a DC motor, then it may run on anything from 96 to 192 volts. Many of the DC motors used in
electric cars come from the electric forklift industry.
DC installations tend to be simpler and less expensive. A typical motor will be in the 20,000-watt to
30,000-watt
range. A typical controller will be in the 40,000-watt to 60,000-watt range (for example, a 96-volt controller
will deliver a maximum of 400 or 600 amps). DC motors have the nice feature that you can overdrive them (up to a
factor of 10-to-1) for short periods of time. That is, a 20,000-watt motor will accept 100,000 watts for a short
period of time and deliver 5 times its rated horsepower. This is great for short bursts of acceleration. The
only
limitation is heat build-up in the motor. Too much overdriving and the motor heats up to the point where it
self-destructs.
Right now, the weak link in any electric car is the batteries. There are at least six significant problems with
current lead-acid battery technology:
- They are heavy (a typical lead-acid battery pack weighs 1,000 pounds or more).
- They are bulky (the car we are examining here has 50 lead-acid batteries, each measuring roughly 6 inches x 8 inches x 6 inches).
- They have a limited capacity (a typical lead-acid battery pack might hold 12 to 15 kilowatt-hours of electricity, giving a car a range of only 50 miles or so).
- They are slow to charge (typical recharge times for a lead-acid pack range between four to 10 hours for full charge, depending on the battery technology and the charger).
- They have a short life (three to four years, perhaps 200 full charge/discharge cycles).
- They are expensive (perhaps $2,000 for the battery pack shown in the sample car).
9. How do I measure State-of-Charge of my batteries
Voltage Method
Measuring state-of-charge by voltage is the simplest method, but it can be inaccurate. Cell types have
dissimilar chemical compositions that deliver varied voltage profiles. Temperature also plays a role. Higher
temperature raises the open-circuit voltage, a lower temperature lowers it, and this phenomenon applies to
all chemistries in varying degrees.
The most blatant error of voltage-based SoC occurs when disturbing the battery with a charge or discharge.
This agitation distorts the voltage and no longer represents the true state-of-charge. To get accurate
measurements, the battery needs to rest for at least four hours to attain equilibrium; battery manufacturers
recommend 24 hours. Adding the element of time to neutralize voltage polarization does not sit well with
batteries in active duty. One can see that this method is ill suited for fuel gauging.
Each battery chemistry delivers a unique discharge signature that requires a tailored model. While voltage-based SoC works reasonably well for a lead acid battery that has rested, the flat discharge curve of nickel- and lithium-based batteries renders the voltage method impracticable. And yet, voltage is commonly used on consumer products. A “rested” Li-cobalt of 3.80V/cell in open circuit indicates a SoC of roughly 50 percent.
The discharge voltage curves of Li-manganese, Li-phosphate and NMC are very flat, and 80 percent of the stored energy remains in this flat voltage profile. This characteristic assists applications requiring a steady voltage but presents a challenge in fuel gauging. The voltage method only indicates full charge and low charge and cannot estimate the large middle section accurately.
Lead acid has diverse plate compositions that must be considered when measuring SoC by voltage. Calcium, an additive that makes the battery maintenance-free, heat raises the voltage by 5–8 percent. Temperature also affects the open-circuit voltage; heat raises it while cold causes it to decrease. Surface charge further fools SoC estimations by showing an elevated voltage immediately after charge; a brief discharge before measurement counteracts the error. Finally, AGM batteries produce a slightly higher voltage than the flooded equivalent.
When measuring SoC by open circuit voltage, the battery voltage must be truly “floating” with no load present. Installed in a car, the parasitic load present makes this a closed circuit voltage (CCV) condition that will falsify the readings. Adjustments must be made when measuring SoC in the CCV state by including the load current in the calculation. In spite of the notorious inaccuracies, most SoC measurements rely on the voltage method because it’s simple. Voltage-based state-of-charge is popular for wheelchairs, scooters and golf cars.
10. How can I get more range out of my EV
- Maintain Your Car - Ensure tire pressures are kept high to ensure reduced rolling resistance. Ensure that your batteries, controller and motor are kept as cool as possible.
- Drive Accordingly - Try to choose a less steep gradient for your route. When pressing the accelerator, use a more gradual approach. Don't have a "heavy foot". Focus on good driving habits. Don't speed from stop light to stop light.
- Adjust Charging Time - It's all too easy to arrive
home in the evening, plug your car in and immediately start it
charging for the next day's commute. But while you'll know your car
will be fully charged when you need it, you may be reducing your
car's available range.
That's because most plug-in cars on the market today slowly self-discharge when they've finished charging, either through battery cell balancing or through natural chemical processes occurring within the battery pack. Over time, this practice can slowly affect your car's battery pack. In fact, allowing your car to sit for hours at a full state of charge is something that many automakers—including Tesla, Nissan, Ford and Mitsubishi—advise against.
While it makes a minimal difference, scheduling your charge to finish charging just before you drive it can give you a few extra miles of range— compared to a car that sat with a full battery pack for many hours. (It's also better for the long-term health of the battery, and allows you to make use of cheaper time-of-use rates.)
11. How do the EV batteries work and how how much do they typically cost & weigh
- How Electric Car Batteries Work?
- Cost & Weight
- A typical 6V golf cart battery (lead acid) such as a Trojan T-105 with a 2 hour Amp-Hour Rating of 146 will weigh 62 lbs. and cost approximately $140-$150.
- A typical Lithiom-Ion battery used for EV's such as a CALB/SkyEnergy 3.2 V with a 100 Amp-Hour capacity weighs 7.1 lbs and costs about $140-$150. Some Lithium-Ion batteries depending on the brand and model can be 2 to 3 times as much!
A battery is a device for storing chemical energy and converting that chemical energy into electricity. A battery is made up of one or more electrochemical cells, each of which consists of two half-cells or electrodes. One half-cell, called the negative electrode, has an overabundance of the tiny, negatively charged subatomic particles called electrons. The other, called the positive electrode, has a deficit of electrons. When the two halves are connected by a wire or an electrical cable, electrons will flow from the negative electrode to the positive electrode. We call this flow of electrons electricity. The energy of these moving electrons can be harnessed to do work -- running a motor, for instance. As electrons pass to the positive side, the flow gradually slows down and the voltage of the electricity produced by the battery drops. Eventually, when there are as many electrons on the positive side as on the negative side, the battery is considered 'dead' and is no longer capable of producing an electric flow.
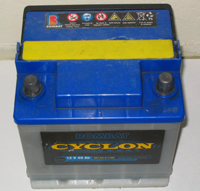
Lead-acid batteries, similar to the one shown here, have been used in automobiles since the middle of the 19th century.
The electrons are generated by chemical reactions, and there are many different chemical reactions that are used in commercially available batteries. For example, the familiar alkaline batteries commonly used in flashlights and television remote controls generate electricity through a chemical reaction involving zinc and manganese oxide. Most alkaline batteries are considered to be a disposable battery. Once they go dead, they're useless and should be recycled. Automobile batteries, on the other hand, need to be rechargeable, so they don't require constant replacement. In a rechargeable battery, electrical energy is used to reverse the negative and positive halves of the electrochemical cells, restarting the electron flow.
Automobile manufacturers have identified three types of
rechargeable battery as suitable for electric car use. Those
types are lead-acid batteries, nickel metal
hydride (NiMH) batteries, and
lithium-ion (Li-ion) batteries.
Lead-acid
Advantages: This chemistry has been proven over more than
140 years. Batteries of all shapes and sizes, available in
sealed and maintenance-free products, are mass-produced today.
In their price range, lead-acid batteries provide the best value
for power and energy per kilowatt-hour, have the longest life
cycle and a large environmental advantage in that they are
recycled at an extraordinarily high rate. (Ninety-seven percent
of the lead is recycled and reused in new batteries.). No other
chemistry can touch the infrastructure that exists for
collecting, transporting and recycling lead-acid batteries.
Disadvantages: Lead is heavier compared to some alternative elements used in other technologies; however, certain efficiencies in current conductors and other advances continue to improve on the power density of a lead-acid battery's design.
Lithium-ion
Advantages: It has a high specific energy (the number of
hours of operation for a given weight) making it a huge success
for mobile applications such as phones and notebook computers.
Disadvantages: More expensive than lead. The cost differential is not as apparent with small batteries for phones and computers, and owners of these devices may not realize that they are paying much more per stored kilowatt hour than other chemistries. However, because automotive batteries are larger, the cost becomes more significant. In addition, currently there is no established system for recycling large lithium-ion batteries.
Nickel-metal hydride
Advantages: It is reliable and lightweight. In hybrid
vehicles, these batteries have equal to 100,000 miles.
Disadvantages: The metals in the battery are 25 times more expensive than lead. Nickel has been identified as a carcinogen. Hybrid vehicles have not been on the road long enough to allow the batteries to completely prove their projected cycle life. No significant recycling capability exists.
Note: The Advanced Lead-Acid Battery Consortium has helped to develop and test an advanced lead-acid battery powered system that operates at the partial state of charge demands necessary for a hybrid vehicle and recently equipped a Honda Insight with this system. Advanced lead-acid batteries will challenge the more expensive nickel metal hydride system in hybrid vehicles today.
Lead-acid batteries were invented in 1859 and are the oldest form of rechargeable battery still in use. They've been used in all types of cars -- including electric cars -- since the 19th century. Lead-acid batteries are a kind ofwet cell battery and usually contain a mild solution of sulfuric acid in an open container. The name comes from the combination of lead electrodes and acid used to generate electricity in these batteries. The major advantage of lead-acid batteries is that, they are well understood and cheap to produce. However, they do produce dangerous gases while being used and if the battery is overcharged there's a risk of explosion.
Nickel metal hydride batteries came into commercial use in the late 1980s. They have a high energy density -- that is, a great deal of energy can be packed into a relatively small battery -- and don't contain any toxic metals, so they're easy to recycle.
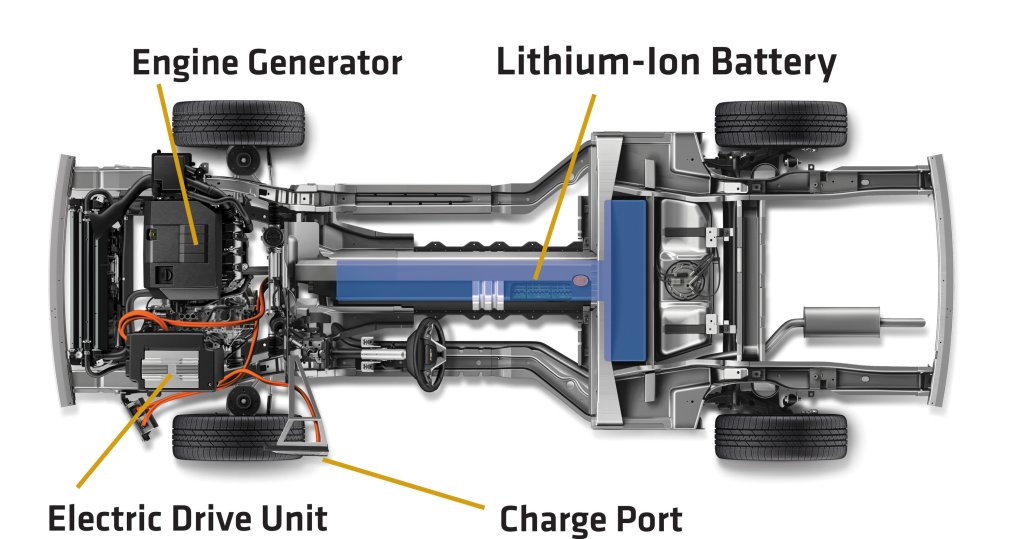
© GM Corp.
This Chevy Volt concept vehicle chassis clearly shows the location of the vehicle's lithium-ion battery pack (in blue).
Lithium-ion batteries, which came into commercial use in the early 1990s, have a very high energy density and are less likely than most batteries to lose their charge when not being used -- a property called self discharge. Because of their light weight and low maintenance requirements, lithium-ion batteries are widely used in electronic devices such as laptop computers. Some experts believe that lithium-ion batteries are about as close as science has yet come to developing a perfect rechargeable battery, and this type of battery is the best candidate for powering the electric cars of the near future. A variation on lithium-ion batteries, called lithium-ion polymer batteries, may also prove valuable to the future of EVs. These batteries may eventually cost less to build than lithium-ion batteries; however, at the present time, lithium-ion polymer batteries are prohibitively expensive.
12. What should I know about battery care
Any electric car that uses batteries needs a charging system to recharge the batteries. The charging system has two goals:
- To pump electricity into the batteries as quickly as the batteries will allow
- To monitor the batteries and avoid damaging them during the charging process
The most sophisticated charging systems monitor battery voltage, current flow and battery temperature to minimize charging time. The charger sends as much current as it can without raising battery temperature too much. Less sophisticated chargers might monitor voltage or amperage only and make certain assumptions about average battery characteristics. A charger like this might apply maximum current to the batteries up through 80 percent of their capacity, and then cut the current back to some preset level for the final 20 percent to avoid overheating the batteries.So here are my proven recommendations on how to take care of these batteries:
- Always fully recharge them as soon as possible after use. Do not leave them even only slightly discharged for long periods of time.
- Maintain a trickle charge current on the battery at all time when not in use. A DC current of 10mA (ten
milliamps) is sufficient to keep the battery fully charged up indefinitely, but is small enough that it
will not cause any evaporation or wear. I am not describing a charging method here, just a trickle
current. This is the circuit I am using. When the battery is connected, the LED turns on. When there is
a power outage, the LED does its diode work and stops the battery from discharging back into the
charger.
With that said, here are some proven recommendations on how to better care for your batteries:
- Never store a battery on a concrete floor, or directly on any floor. This may cause a temperature gradient inside the battery and will accelerate aging. Use thick pieces of wood (2x4 OK) or even better, store it on a table, away from the cold floor.
- Never discharge a battery to less than 80% of its nominal voltage. For a 12.6 VDC battery, this is 10.0 VDC. This is applicable also to Deep-Cycle batteries. These batteries, contrary to what their naming suggests, do not like a deep discharge.
For batteries that need maintenance, the battery should be cleaned using a baking soda and water solution; a
couple of table spoons to a pint of water. Cable connections need to be cleaned and tightened as battery
problems are often caused by dirty and loose connections. A serviceable battery needs to have the fluid level
checked. Use only mineral free water, Distilled is best as all impurities have been removed, and there is
nothing left that could contaminate your cells. Don't overfill battery cells especially in warmer weather
because the natural fluid expansion in hot weather can push excess electrolytes from the battery.
To prevent corrosion of cables on top post batteries use a small bead of silicone sealer at the base
of the post and place a felt battery washer over it. Coat the washer with high temperature grease or petroleum
jelly (Vaseline), then place cable on the post and tighten. Coat the exposed cable end with the grease. Most
folks don't know that just the gases from the battery condensing on metal parts cause most corrosion.
13. Can I use an automatic transmission
Most EV conversions are manual transmissions because they are more efficient than automatic transmissions and provide greater range, require less motor torque, require no transmission cooler, and are easier to convert. The problem with an automatic transmission is that it shifts at about 2000 rpm; the electric motor is usually designed to operate efficiently between 4000-5000 rpm. Consequently, the automatic transmission is a poor choice which results in decreased range. If you buy a vehicle with an automatic transmission, you can replace it with a manual transmission. The additional cost is $150 and up depending on the transmission and used auto parts dealer. Consider trading the automatic transmission.
Made in the USA
The only DC Motors Manufacturer in America
Fast, Reliable Shipping
We provide fast 2-3 day shipping in the USA
Engineering Expertise
Unparallel customer support from our expert engineers